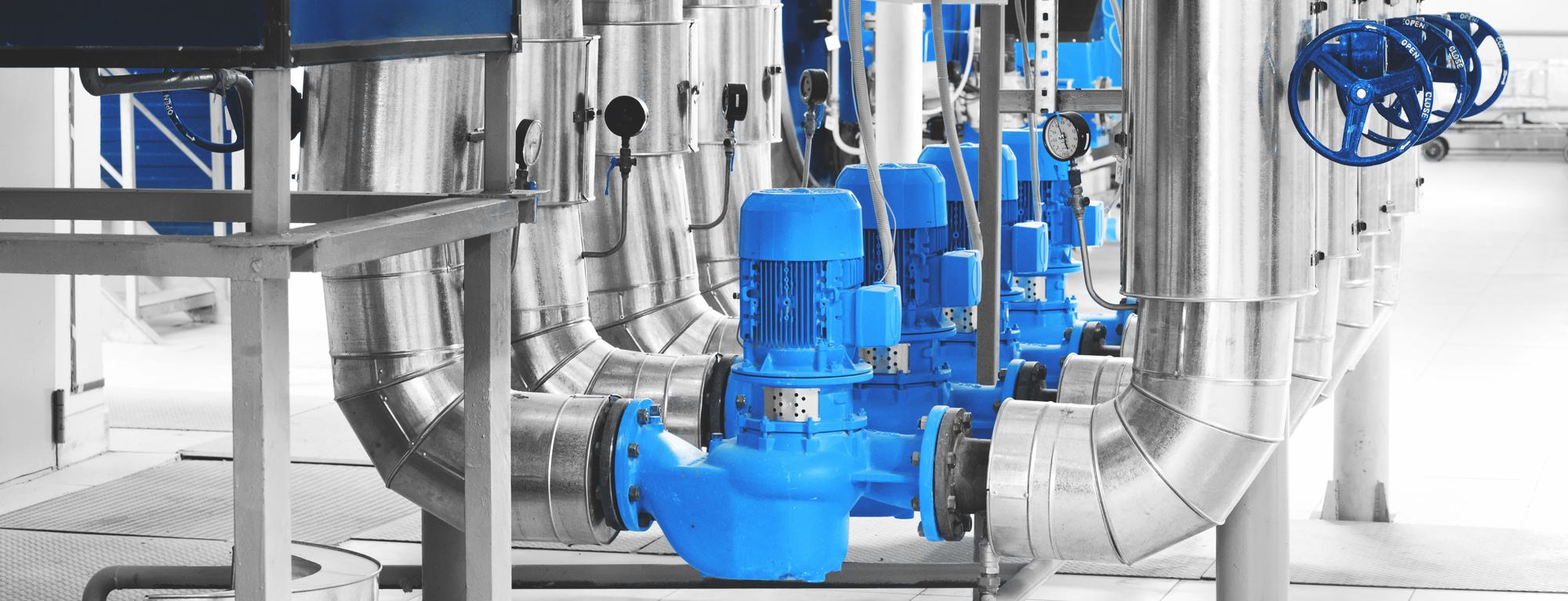
Selecting the right liquid transfer pump for an industrial application is no small decision. The consequences of choosing poorly can be spilled chemicals, damaged equipment, and unnecessary costs.
But don’t sweat it too much. Picking the optimal pump for handling your specific liquid doesn’t need to be overwhelming. Follow the steps outlined below to find the ideal liquid transfer solution for your facility.
- Define Your Needs
When selecting a liquid transfer pump, the first step is figuring out exactly what you need it to do. Start by looking at the properties of the fluid you’ll be pumping.
- Is it thick like syrup or thin like water?
- What temperature will it be at?
- Does it have abrasive particles or chemical characteristics that could damage pump components?
Understanding viscosity, temperature, and other fluid properties will guide you toward pumps designed to handle that specific liquid.
Next, think about the flow rate and discharge pressure your process requires. Are you trying to fill a tank quickly or precisely meter a chemical? The flow rate and pressure capabilities of different pump types can vary widely, so pin down your ideal numbers.
- Finally, consider the suction and discharge distances.
- How far will the fluid be drawn vertically on the intake side?
- Will the output need to push liquid 20 feet in the air or just a few inches?
- Suction lift and discharge head impact pump selection.
Defining these key fluid and application needs upfront ensures you choose a pump sized for the job.
- Explore Pump Types
With your fluid properties and flow requirements defined, you can start exploring different types of liquid transfer pumps.
Centrifugal pumps are great for large flow rates of thinner, non-viscous liquids like water. The fast-spinning impeller generates flow by slinging liquid outward. Centrifugal models are affordable and efficient, but can’t handle thick fluids or provide precise flow control.
Positive displacement pumps are the go-to for viscous liquids like oils or chemicals. The tight clearances and rotating gears provide excellent suction and accurate metering. However, flow rates are typically lower than centrifugal designs.
Rotary vane and gear pumps offer versatility to handle both thin and viscous liquids. They provide more precision than centrifugals but higher flow rates than positives. The tradeoff is higher cost for these sophisticated designs.
With pump experts such as KNF or others you prefer on your side, it’ll only be a matter of time until you find the best for your business.
- Efficiency In Mind
When selecting a pump, it’s wise to think about efficiency and how to get the most bang for your buck. Matching the pump technology and horsepower to your specific needs minimizes wasted energy and costs.
For low-flow applications, a centrifugal pump may be overkill. Opt for a positive displacement design sized closer to your flow rate. The smaller motor will save on energy bills while still meeting requirements.
Consider the power source too. Can you take advantage of an existing compressed air system and use an air-operated double diaphragm pump? The energy savings compared to an electric motor may be substantial.
Do your homework on pump efficiency curves and optimal operating ranges. A high-efficiency model like a regenerative turbine pump can pay for itself over time through energy savings. Keep efficiency in mind from the start.
- Maintenance Ease
When selecting a pump, consider how easily it allows access for cleaning and inspections. Look for quick disconnect piping and minimal disassembly to reach internal components. Being able to thoroughly clean a pump prevents buildup that leads to wear and failure down the road.
For critical applications, choose self-priming pumps that can be pulled for maintenance while system operations continue. There are even magnetic drive pumps that eliminate seals, allowing the impeller to be removed without spillage for cleaning.
And since you’re dealing with pumps and chemicals, make sure you put safety first.
- Safety First
Here’s the deal when picking a pump – you’ve got to make safety the number one priority.
- Look for pumps with built-in features that prevent accidents and spills.
- Pressure relief valves are essential for releasing excess pressure from a blocked discharge line or dead-headed pump. This protects piping from rupture and personnel from injury.
- Leak detection like sealed capsules that indicate a damaged seal will alert you to address minor issues before they become major problems.
- Carefully review chemical compatibility and temperature limits before purchase.
Okay, you may be thinking: isn’t all this safety measures expensive up front? It is, but compared to cleaning up a toxic spill or OSHA violation? You’re better off putting safety first.
Wrapping It Up
Do yourself a favor and take the time upfront to really understand your pumping needs. Give the tips in this guide while you’re at it. With solid homework, asking questions, and tapping manufacturers’ expertise, you’ll very likely land on the ideal pump for your specific situation.